Fiber Optic Cabling Safety and Inspection
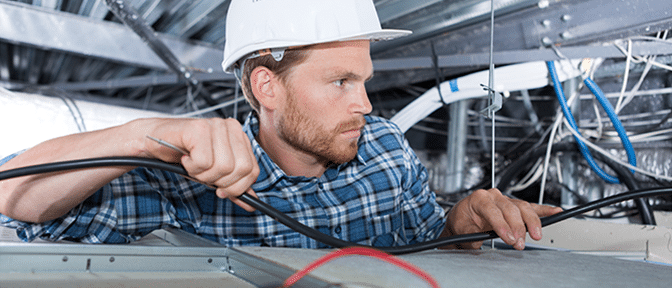
Tags: cabling | fiber optic | installation | safety | Testing | training
This article covers the procedures required to work safely with fiber optic components as well as some general information.
General Laser Background
Lightwave/fiber optic systems, their associated test sets, and similar operating systems use semiconductor laser transmitters that emit light at wavelengths of 850 nm or 0.85 micrometer and greater. The emitted light is below the red end of the visible spectrum. This is in the near-infrared portion of the spectrum, which is not normally visible to the human eye. Although light at the near-infrared wavelengths is officially designated as invisible, some people can see it even at low power levels (levels several orders of magnitude below any that have been shown to cause injury to the eye). Consequently, lasers and laser products are subject to regulations for safe operation and use.
How Lasers Work
The word “laser” is an acronym for Light Amplification by Stimulated Emission of Radiation, and it describes the physical process by which light is amplified. Light, that slender portion of the entire electromagnetic spectrum that is visible to the eye, is generally defined as “white” light, the radiation that can be seen.
All lasers can produce an intense beam of monochromatic light. The term monochromaticity means a single wavelength output of pure color that may be visible or invisible to the eye. A laser produces a small-diameter beam of light and, because the beam diameter is small, the power density is very high. The power density, or power per unit area, is called irradiance. Very high values of irradiance are associated with the practical uses of the laser in industry for cutting, drilling, hardening, levelling, and aligning various materials. Lasers are also used in medicine for various surgical procedures, including eye surgery.
A conventional laser beam expands very little over distance, or is said to be very well collimated. Thus, conventional laser irradiance remains relatively constant over distance. However, lasers used in lightwave systems have a large beam divergence, typically 10 to 20°. In this case, irradiance obeys the inverse square law (doubling the distance reduces the irradiance by a factor of 4) and rapidly decreases over distance.
Lasers and Eye Damage
Light energy emitted by lasers and high-radiance LEDs may cause eye damage if absorbed by the retina. When a beam of light enters the eye, the eye magnifies and focuses the energy. The irradiance of the beam at the cornea is amplified approximately 100,000 times at the retina. Thus, a beam of fairly low power entering the eye can have a very high irradiance at the retina and can cause permanent eye damage. The damage threshold is related to the maximum safe radiation level of the cornea, the surface of the eye.
The damage mechanism at the wavelengths used in telecommunications is thermal in origin. Damage is caused by heating, not by chemical change. Therefore, a specific amount of energy is required for a definite period of time to heat an area of retinal tissue. Damage is not instantaneous. It occurs only when one looks at the light so long that the product of the light energy and the viewing time exceeds the damage threshold (maximum safe radiation level at the cornea). For wavelengths used in telecommunications, these values are defined as 10 mW for 10 seconds and 5.6 mW for 100 seconds. Wavelengths at or greater than 1400 nm have higher damage thresholds, and thus are safer, because the eye is opaque to these longer wavelengths.
Classification of Lasers
Regulations require manufacturers to certify each laser or laser product as belonging to a class. The following classification from the United States are also used in many other countries. A laser is certified to belong to one of four major classes: 1, 2 or 2a, 3a or 3b, or 4. Lasers are classified according to the accessible emission limits and their potential for causing injury.
Fiber Optic Safety Precautions
Important Notice: The following describes safety from a “good practice” point of view and can be applied to your work environment. National or Regional regulations however may be more detailed and may require additional measures in order to meet your local safety and labor protection rules.
Classification of Fiber Optic Equipment
Lightwave systems use a transmitter with a laser of usually class 3b. The fiber connection between front panel fiber coupling to the laser itself is usually a fiber pigtail. As most loss in a lightwave system is encountered in the laser to fiber coupling, a totally enclosed system presents no risk of eye injury. Such an enclosed system can therefore be classified to class 1.
The fiber optic cables that interconnect various components in a lightwave system can disconnect or break and may expose people to lightwave emission. Also, certain measurement and maintenance procedures may expose the technician to emission from the semiconductor laser during installation and servicing. Unlike that of more familiar devices, such as solid-state and gas lasers, the emission pattern of a semiconductor laser results in a highly divergent beam. In a divergent beam, the irradiance (power density) dissipates rapidly with distance. The greater the distance, the less potential risk for eye injury. Energy from the end of a fractured fiber is more divergent than energy from a fiber end that is polished flat.
Inadvertently viewing an unterminated or damaged fiber with the unaided eye at distances greater than 5 to 6 inches (12.7 to 15.24 cm) does not cause eye injury. However, damage can occur if an optical instrument such as a microscope, magnifying glass, or eye loupe is used to view the energized fiber end. Indirect image converters, also known as an Infrared (IR) scope, are safe for viewing.
Although viewing an unterminated, energized connector or a damaged fiber end with the unaided eye at distances greater than a few inches (centimeters) does not cause eye injury, nonetheless, it should always be avoided. Therefore, appropriate safety precautions are required to protect employees from accidental exposure to lightwave emission.
Safety Precautions for Enclosed Systems
Under normal operating conditions, lightwave transmission systems are completely enclosed; nonetheless, the following precautions should be observed:
- Because of the potential for eye damage, technicians should not disconnect any fiber optic cable or splices and stare into the optical connectors terminating the cables.
- Under no circumstances should lightwave/fiber optic operations be performed by a technician before satisfactorily completing an approved training course.
- Since viewing lightwave emission directly with an optical instrument such as an eye loupe greatly increases the risk of eye damage, an appropriate label must appear in plain view on the front of the main frame or fiber optic termination/ interconnection equipment. The label should read:
NOTICE: UNTERMINATED OPTICAL CONNECTORS MAY EMIT LASER RADIATION. DO NOT VIEW THIS BEAM WITH OPTICAL INSTRUMENTS.
Safety Precautions for Unenclosed Systems
During service, maintenance, or restoration, a lightwave transmission is considered unenclosed. Under these conditions, follow these practices:
- Only authorized, trained personnel should be permitted to perform service, maintenance, and restoration. Considerable effort should be taken to avoid exposing the eye to emissions from unterminated, energized optical connectors at close distances.
- Only authorized, trained personnel should be permitted to use the lightwave test equipment during installation and/or servicing since this equipment contains semiconductor lasers.
- All unauthorized personnel should be excluded from the immediate area of lightwave transmission systems during installation and service.
Safety Precautions for Accidental Breaks
For accidental breaks in the fiber optic cable or accidental removal of a fiber optic cable from its normal position, the following steps should be followed by non-trained installation and/or service personnel:
- Do not examine or stare into broken, severed, or disconnected fiber optic cables. (Although the NOTICE shown before clearly defines the hazard associated with lightwave transmission systems and specifies appropriate safety precautions, all eye exposure to lightwave emission should be avoided.)
- Report problems to the supervisor so that arrangements can be made for trained installation or service personnel to repair or replace cables.
- View broken cables only with an indirect image converter unless it has been verified that all lightwave emissions are turned off.
- During all splicing operations that require viewing the end of the fiber, it is mandatory that all lightwave sources on the fibers involved be de-energized.
The trained personnel for restoring accidental breaks in the fiber optic cable and installation crews should follow safety practices as well. The following steps should be taken to insure safe work environments:
- View fibers only if you can determine it is inactive,( all eye exposure to lightwave emission should be avoided.)
- It is the employees responsibility to work according to the safety practices and take precautions. Absence of safety equipment (e.g. safety glasses) and other safety issues must be reported to a responsible supervisor.
- A supervisor is responsible for maintaining the safety procedures and to take care all appropriate tools and equipment are present.
- View broken cables only with an indirect image converter, unless it has been verified that all lightwave emissions are turned off.
- During all splicing and connectorizing operations that require viewing the end of the fiber, it is mandatory that all lightwave sources on the fibers involved be de-energized.
Eye Protection
Safety glasses must be worn AT ALL TIMES when working with cable, fiber, and/or chemicals. Ultraviolet glasses should be worn when using ultraviolet lamps.
Fiber/Cable Safety
Fiber ends are sharp and can easily penetrate skin and clothing. This is particularly true when the protective coating is removed from the fiber. Optical fibers are small in diameter. Care should be exercised when cleaving fibers and disposing of the pieces of fiber which have been cut off in a waste receptacle.
If you are interested in learning more, take a look at the Network Project Planning and Safety or Network Test and Inspection courses.
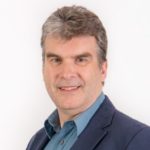
Written by James Donovan
You might also enjoy
FO Connector Contamination – A Constant Threat
Fiber optic communication most commonly works in duplex or multifiber transmission by transmitting light to a receiver in one direction on a fiber and receiving transmitted light back to a second receiver on the second fiber. Most engineers can understand that and...
Why Inspect and Clean Fiber Optic Connectors?
Inspecting and cleaning of fiber optic connectors during installation and when making any patching, is essential. Any contamination on a patch cord connector will be transferred through the coupler to the connector it is mated to. Even when testing fibers with a test...
Cleaning MPOs
MPO connectors should always be inspected with a scope before they are used, be that on a patch cord or a bulkhead. If they need to be cleaned, one-click cleaners are keyed to ensure the tip only fits one way onto the connectors and is able to clean both male and...