Deploying Fiber Optic Cabling in Industrial Environments
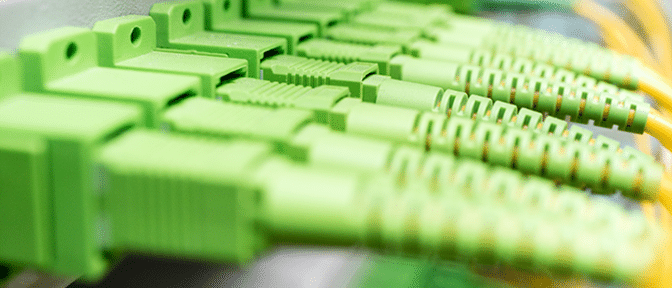
Tags: design | factory | installation | network
Industrial environments lend themselves to fiber optic cabling as the communications medium of choice, with copper cabling limited to local equipment connection. In this environment fiber optic cabling offers significant advantages over alternative distribution systems. This article looks at the advantages of fiber optic cables and apparatus products in industrial environments, and discusses design considerations specific to this environment.
Industrial environments are often characterized by extremes of heat, humidity, and abuse. Many primary manufacturing functions, such as steel, aluminum and glass, generate enormous amounts of heat during the manufacturing process as do welding and other production processes. Heat, dust, induced currents, lightning, rodents, corrosive fluids and mechanical force represent the most significant threats to any cable plant.
Advantages of a fiber Optic Network
There are many compelling reasons to choose optical fiber for an Industrial cabling network.
Increased bandwidth refers to the ability of fiber to deliver data rates spanning across the full range from kilobits to megabits to multiple gigabits per second. No other media can provide this range, making fiber the most future-proof media available.
Optical fiber provides broad applications coverage. Fiber is a native media to virtually all data applications with products available from a large number of vendors.
Fiber makes administration easier because its increased distance capability allows fiber cabling designs to use fewer cross connects. In fact, fiber’s distance and bandwidth capability allow most buildings to be cabled with only a single cross connect. This single point administration architecture allows all hubs to be centrally located providing easy work group administration.
Fewer cross connects and centralized hubs also reduce maintenance activities. Fewer connections mean fewer places where things can go wrong. Centralizing equipment eliminates the need to provide and maintain clean power and environmental conditioning in closets.
Large operating margins, immunity from radio frequency interference and lightning strikes, and robust cable designs give fiber networks increased reliability. Despite its lightweight and small diameter, fiber cable’s tensile strength and crush resistance far exceed other cabled media. This robustness reduces the chance of damage during installation and network reconfigurations. Better network reliability results in higher productivity and fewer disruptions.
Optical fiber’s low loss and high bandwidth allow the network to cover long distances. LAN standards specify multimode fiber links with distance capability sufficient to cover most campus wide networks. For longer distances, singlemode fiber and electronics commonly deliver signals up to 40 kilometers (25 miles). Within a single building, the high bandwidth of multimode fiber allows multi-gigabit data rates and streamlined architectures with a single point of administration.
Fiber networks have no electromagnetic compatibility (EMC) concerns. Because fiber transmits information with light instead of electricity, it is not susceptible to radio frequency interference.
Most fiber cables are constructed without metallic elements, they do not attract or conduct lightning. Several outside plant cable designs and virtually all inside plant cable designs are all-dielectric (non-metallic) constructions. Lightning immunity improves network reliability, reduces equipment damage, and eliminates protection issues.
Lastly, the non-conductive nature of fiber eliminates grounding concerns on data communications cables. In large buildings and campuses, differences in ground potential can cause unwanted currents to flow in metallic communications cables. This leads to concerns over how to properly ground communications systems to avoid data corruption and equipment failure, and ensure personal safety. In electric power utilities, the huge currents produced by electric generating equipment can cause very large ground potential differences, as can the large currents consumed by heavy electric machinery in manufacturing environments. Here again fiber provides the best and safest solution.
Cabling Architectures and Design Considerations for the Industrial Environment
The right architecture is one that meets the needs of the users in the most efficient way. Many issues must be addressed when choosing an industrial cabling design. Among them are the structure of the building and the way the building is occupied. Others involve considerations about the network services required now and into the future.
For the design of the cabling system in an industrial environment, two extra sub systems are added to the standard areas one would consider for a cabling solution (i.e. Work Area, Horizontal, Building Backbone, Campus Backbone, Administration Sub Systems). The additional sub systems are the Industrial Backbone and the Industrial Subnet.
Industrial Backbone
The industrial backbone level is the primary infrastructure of the industrial plant cabling. The industrial backbone is comprised of a series of fiber optic segments and cross-connects configured such that there is always physical redundancy of fiber optic cable. In addition, the fiber optic cables must also be diversely routed. This configuration creates a mixture of star wired and physical ring or hierarchy of rings for the industrial backbone. The industrial backbone provides highly reliable physical connectivity for critical applications.
Each logical network within the industrial backbone communicates over separate optical fiber strands. More than one industrial backbone level may exist on a premise. This is often the case in campus environments where there will be a plant-wide backbone and a building-wide backbone or even within a building where there may be a building-wide and an area-wide backbone. The requirements for all remain the same: the cabling must be optical fiber and configured with physical redundancy and diversity.
The redundancy of the industrial backbone addresses the high reliability requirements in the industrial environment by always offering an alternate and diversely routed path for communications. In the event of a cable or equipment failure, traffic can be rerouted via a manual patch or rerouted automatically with active electronics.
Industrial Subnets
The industrial subnet is the cabling and associated cross-connect hardware and faceplates that provide connectivity to end point equipment without alternate or diverse routing. The physical topology of the industrial subnet is a star or hierarchical star.
The media of the industrial subnet may vary. It may consist of fiber or copper cabling. The media selection is dependent on the environment and the application. Transmission over greater distances require optical fiber, but if connectivity requirements are within 100 meters of an administration point, copper cabling may be used as in a typical office building design, but consideration must be given to the physical and electrical environment when selecting the routing, protection and termination of the cabling.
General Design Considerations
Each industrial site has its own unique requirement and the level of automation from one manufacturing site to another varies dramatically. However the design architecture is consistent among all installations and the process should follow the following procedure:
Data Collection
A cabling system for the industrial environment may be designed with specific requirements in mind or to provide a ‘generic’ distribution system for a facility. In the first case a significant level of detail should be available regarding the types of devices to be connected and their associated interface requirements. For a ‘generic’ design, only architectural and environmental information may be available. In either case, the first step in developing any design is to collect as much information as possible about the site.
The end result of the data collection process should include a complete facility layout with potential node locations identified and all equipment locations, quantities, and reliability requirements marked. In addition, a table listing the point to point connectivity requirements for each type of communications interface and type of equipment must be developed in this step.
Physical Design
Physical design for the cabling system can be divided into two levels: high level design and detail level design. The high level design addresses issues related to locating and routing the backbone and subnets while the detail design addresses issues relating to the subsystems such as the exact location and number of cross-connects, size of cables, number of patch cords etc.
Since the design of a cabling system is an iterative process the high level design is completed first, followed by the detail design.
The following guidelines should be observed when locating cross-connects:
- A building that supports a critical process should have at least one backbone cross-connect
- Cross-connect locations should be clean and secure. If necessary, secure equipment rooms should be constructed.
- Often industrial subnet cross-connect fields are out on the factory floor. If so, they should be placed inside an enclosure for protection. If there is heavy traffic in the vacinity (i.e. fork lifts), elevate the cross-connect off the ground.
- Avoid locating cross-connect near potential hazardous or explosive areas.
- Avoid locating cross-connects near large motors or generators. Although fiber is immune to EMI, the electronics are often not.
The data collected in the data collection phase should be used at this point. The overall facility drawing with potential node locations marked should be used to lay-out potential industrial backbone routes. In many cases this can be done by ‘connecting the dots’ representing potential node locations identified during earlier walkthroughs. This process is the same whether this is an existing facility or a new building or plant.
The preliminary routing should then be reviewed to ensure that the design rules are satisfied. For example, if the backbone doesn’t allow rings or redundant paths depending on the reliability level required, potential redundant routes should be identified to complete this. The distance between the nodes and the between the nodes and the main equipment room should be assessed depending upon the application to be supported. The final result should be a backbone cable route connecting all critical points either within a building or across a campus with redundant paths.
For all single point administration architectures sufficient cable slack should exist in the closet to allow any necessary movement of the cables when migrating to a horizontal cross connect. Slack may be stored as cable or fiber. Slack storage should provide bend radius control so that cable and fiber bend radius limitations are not violated. Cable slack may be stored within enclosures or on the walls or cable trays of the closet. Fiber slack (buffered or coated) should be stored in protective enclosures.
Logical Design
The logical design considers the applications and services required in the facility. This part of the design may not be possible in a ‘generic’ design, but some level of expected applications and equipment should be assumed. The following are some rules of thumb to be considered:
- Maintain network protocols in native format
- Select electronics which support industry standards
- Keep separate networks/service types on separate fibers.
- For topologies that support ring or secondary cable routes, separate primary and secondary paths when routing over the industrial backbone.
- For critical applications on the industrial backbone that do not support ring or secondary cable routing, plan redundant rerouting via manual patch.
Validation
Design validation should be performed to ensure that all designs meet certain parameter, for both the physical and logical requirements. The physical validation should be based on application requirements, distances and redundancy requirements. Both singlemode and multimode optical fiber should be installed as standard. Multimode cable segments should be limited to 300 meters where possible to ensure high speed applications can be supported.
The logical validation pertains to the selection and configuration of electronics and services over the physical cable plant. Whenever there are standards for a particular service or protocol, always validate against this standard. When proprietary protocols are involved, vendor specifications are used for validation. The following is a list of issues that are usually addressed for the logical validation:
- Optical parameters (wavelengths, source types etc.)
- Basic configuration
- Power margin analysis
- Loss budgets
- Distance between electronics
- Timing considerations
- Number of stations
- Total length
Cable Sizing and Specification
When sizing and selecting cable the following rules of thumb are useful. They are only guidelines. Since each industrial site has its own unique characteristics, a detailed data collection and design process is required.
- A growth factor of between 50% and 100% is often applied after sizing current needs
- Factors affecting industrial backbone cable sizing include:
- Campus layout
- Campus size (number of buildings)
- Level of automation (amount of computer connectivity)
- Level of redundancy
- Cable type selection is based on environment and cost
- Use a mixture of singlemode and multimode fiber optic
The result of these design steps should be a robust, reliable, flexible cabling solution meeting the needs of the industrial location under consideration.
If you are interested in learning more, take a look at the Network Project Planning and Safety or Fiber Optic Cabling Installation courses.
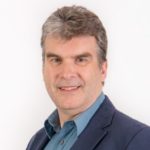
Written by James Donovan
You might also enjoy
FO Connector Contamination – A Constant Threat
Fiber optic communication most commonly works in duplex or multifiber transmission by transmitting light to a receiver in one direction on a fiber and receiving transmitted light back to a second receiver on the second fiber. Most engineers can understand that and...
Why Inspect and Clean Fiber Optic Connectors?
Inspecting and cleaning of fiber optic connectors during installation and when making any patching, is essential. Any contamination on a patch cord connector will be transferred through the coupler to the connector it is mated to. Even when testing fibers with a test...
Cleaning MPOs
MPO connectors should always be inspected with a scope before they are used, be that on a patch cord or a bulkhead. If they need to be cleaned, one-click cleaners are keyed to ensure the tip only fits one way onto the connectors and is able to clean both male and...